Unlocking Potential: The Role of Injection Silicone in Contemporary Business
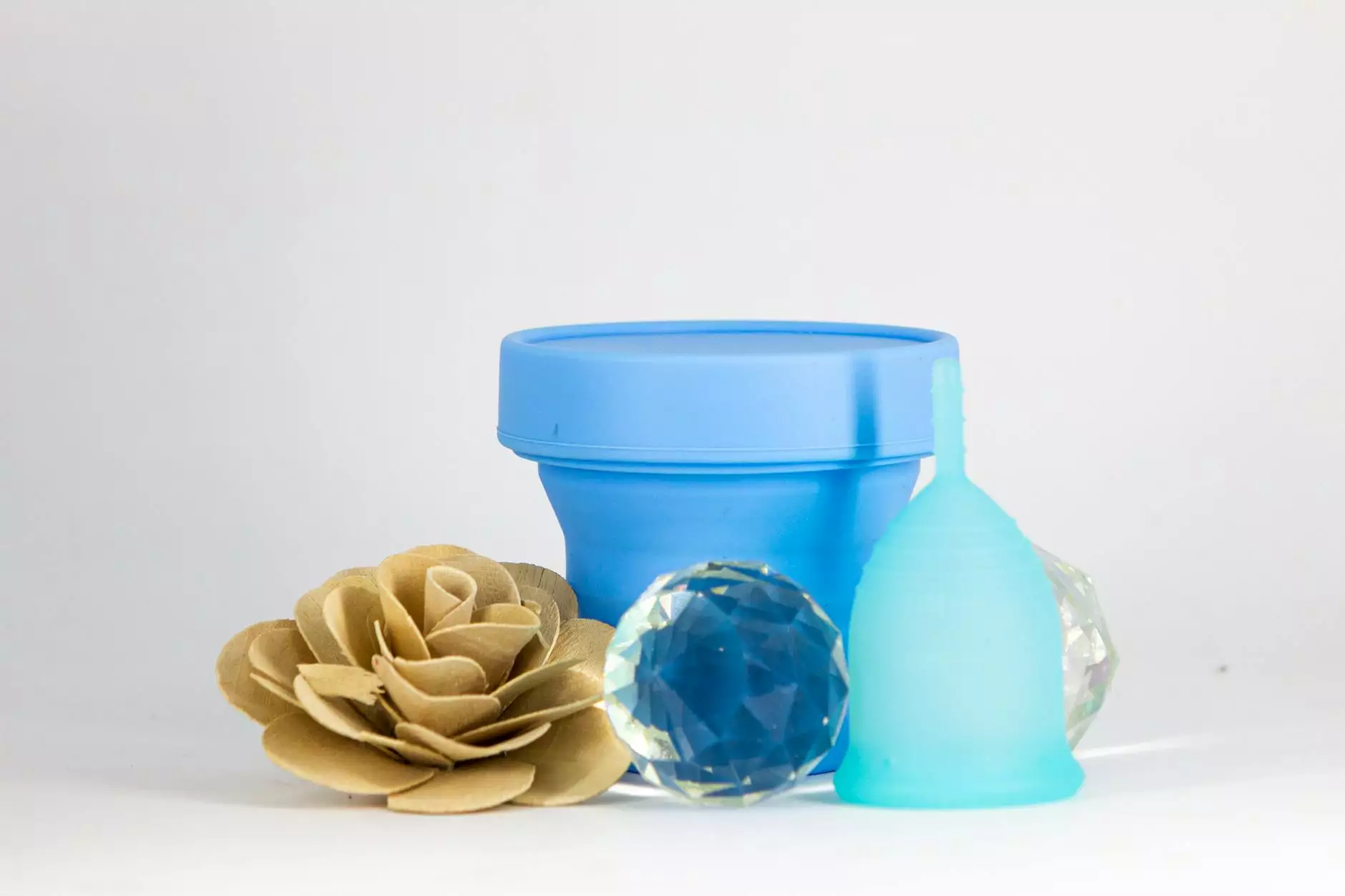
Injection silicone has emerged as a crucial material in various industrial applications, especially in the fields of electronics and medical supplies. This article delves into the vast capabilities of injection silicone, exploring its benefits, applications, and the future it holds in today's technological landscape.
The Fundamentals of Injection Silicone
Injection silicone is a versatile material characterized by its excellent mechanical properties and thermal stability. Created through the process of adding silicone polymers in a controlled injection method, the resulting products are lightweight, durable, and, quite importantly, capable of withstanding extreme temperatures.
Characteristics of Injection Silicone
- High Temperature Resistance: Injection silicone can endure an extensive range of temperatures, making it suitable for both hot and cold environments.
- Durability: It exhibits outstanding resistance to wear and tear, thus extending the lifespan of products.
- Flexibility: This material can be molded into intricate shapes, allowing for innovative designs in product development.
- Non-Toxicity: Particularly in medical applications, injection silicone is safe for use and can be sterilized effectively.
Applications of Injection Silicone in Electronics
In the electronics industry, the demand for robust and reliable materials is ever-increasing. Injection silicone stands out as a material of choice for several reasons:
1. Sealing and Gasketing
Electronics are prone to damage from moisture and dust. Injection silicone provides optimal sealing solutions, ensuring environmental protection for sensitive components. Its inherent flexibility allows it to create perfect seals that withstand pressure.
2. Encapsulation
To enhance durability, electronic parts are often encapsulated in silicone. This protects against chemicals, moisture, and physical impact, ultimately contributing to longevity and reliability in various electronic devices.
3. Vibration Dampening
Many electronic devices generate vibrations that can lead to component failure. Injection silicone helps mitigate these vibrations, providing stabilization and protecting internal circuitry.
4. Heat Management
Effective heat dissipation is vital for optimal electronic performance. Injection silicone can be engineered to provide thermal conductivity, dispersing heat away from critical components.
Transformative Role in Medical Supplies
The medical sector demands precision and safety. The injection silicone process meets these needs, offering distinctive advantages in the production of medical supplies.
1. Medical Devices
From catheters to prosthetics, many medical devices benefit from the use of injection silicone. Its biological compatibility, combined with the ability to maintain a sterile environment, makes it an ideal choice.
2. Soft Touch Surfaces
The tactile experience of medical tools can influence user comfort and satisfaction. Injection silicone can be tailored to create soft-touch surfaces that enhance usability.
3. Disposable Products
In the production of one-time-use medical supplies, such as syringes and gloves, injection silicone offers a non-toxic option that can be safely disposed of after use.
4. Customizable Solutions
With the ability to mold silicone into various shapes, manufacturers can produce customized solutions that fit specific medical needs and enhance patient care.
Advantages of Using Injection Silicone for Businesses
Choosing injection silicone as a primary material can provide numerous advantages for businesses operating in the electronics and medical fields:
1. Cost-Effectiveness
Despite the initial investment, the longevity and durability of products made with injection silicone mean reduced replacement costs over time.
2. Enhanced Product Design
Injection silicone can be molded into complex designs that enhance product functionality, making it a go-to material for innovation.
3. Improved Product Performance
Materials that withstand extreme conditions or perform specific functions improve user satisfaction and device reliability.
4. Regulatory Compliance
With compliance to stringent industry regulations, particularly in medical applications, businesses can ensure safety and quality in their products.
Future Outlook of Injection Silicone in Industries
The future of injection silicone is promising, with ongoing innovations expanding its applications. As industries become increasingly reliant on advanced materials, injection silicone is likely to see growth in:
1. Smart Electronics
As the market for smart devices expands, injection silicone will play a vital role in integrating sensors and other components that require reliable sealing and durability.
2. Biocompatible Materials
Biocompatibility is an area of continuous research. The evolution of injection silicone will enhance its use in more sophisticated medical devices and surgical applications.
3. Sustainable Practices
With an increasing focus on sustainability, the development of eco-friendly silicone materials will align with global efforts towards reducing environmental impact.
4. Custom Manufacturing Technologies
Advancements in manufacturing technologies may lead to more efficient methods for producing products with injection silicone, further enhancing its utility and appeal.
Conclusion
In conclusion, injection silicone proves to be a transformative material, playing an essential role in the manufacturing processes within the electronics and medical supplies sectors. Its unique properties enable businesses to innovate, improve product performance, and meet stringent compliance standards.
As industries continue to evolve, embracing cutting-edge materials like injection silicone will be crucial for maintaining competitive advantages and meeting future challenges head-on.
About Nolato
Nolato is at the forefront of innovative solutions in electronics and medical supplies, continually exploring new ways to incorporate injection silicone into our offerings. By leveraging advanced materials, we aim to deliver products that redefine quality and functionality in modern business applications.