Understanding the Importance of a Reliable PLC Repair Center
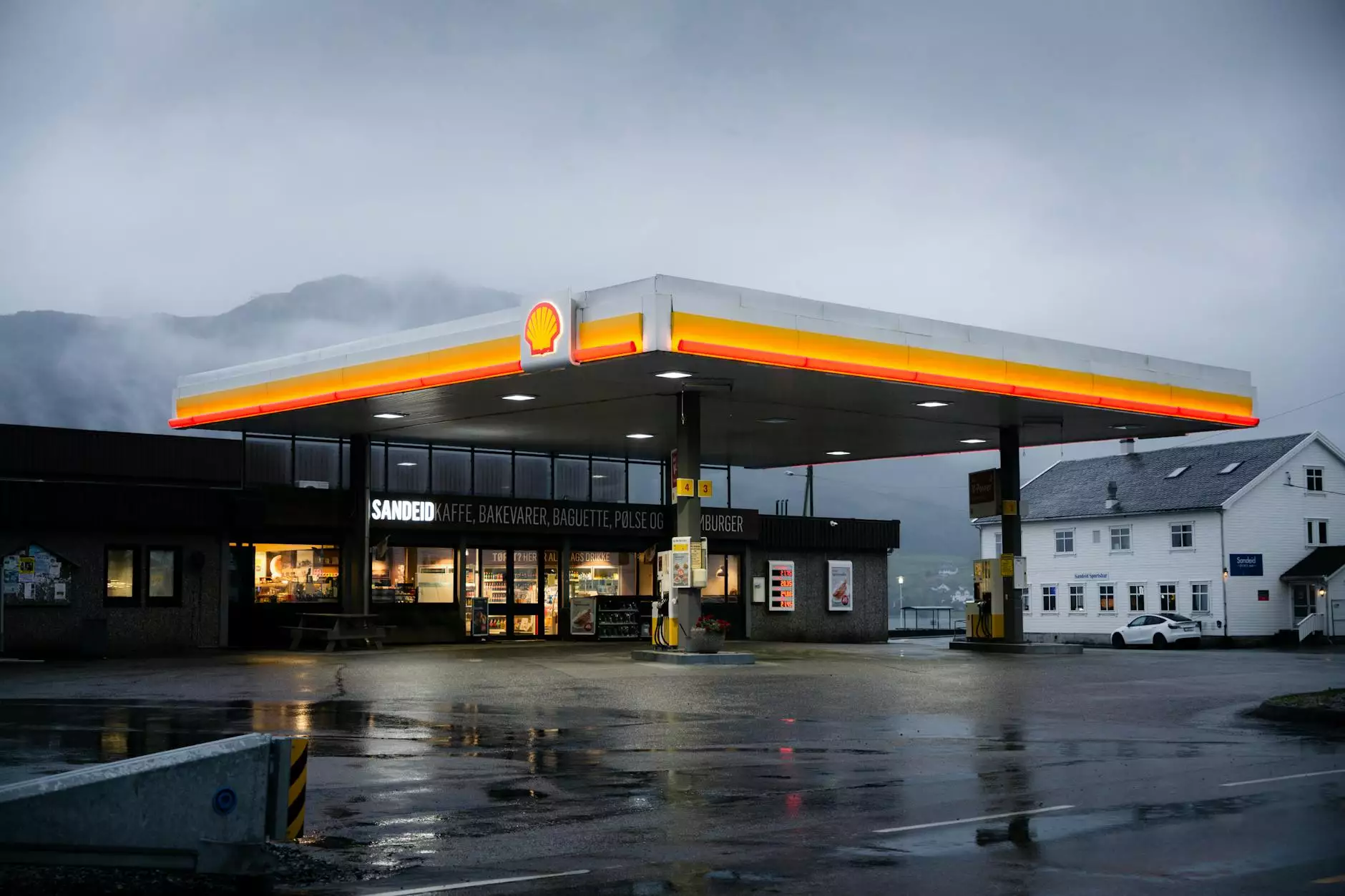
In today's fast-paced industrial landscape, maintaining the efficiency and reliability of automation systems is crucial for businesses aiming to stay competitive. One of the fundamental components in many automation systems is the Programmable Logic Controller (PLC). These devices are the backbone of industrial automation, and any malfunction can lead to significant downtime and financial loss. That's why it is imperative to partner with a reliable PLC repair center to ensure that your systems are running smoothly and efficiently.
The Role of PLCs in Modern Industry
PLCs are industrial digital computers designed for the control of manufacturing processes. With their ability to handle multiple input and output signals, they facilitate automation in a variety of industries, including manufacturing, energy, and transportation. The significance of these controllers cannot be overstated:
- Reliability: PLCs are built to withstand harsh environments, making them a reliable choice for continuous operation.
- Flexibility: PLCs are reprogrammable, allowing companies to adapt to changing production needs without the need for new hardware.
- Efficiency: By automating processes, PLCs significantly improve operational efficiency and reduce the likelihood of human error.
Why Choose a Specialized PLC Repair Center?
Finding a specialized PLC repair center is essential for businesses that rely on these devices. Here are several reasons why specialized services make a difference:
- Expertise: Trained technicians understand the intricacies of various PLC brands and models, providing precise and effective repairs.
- Speed: Quick turnaround times minimize downtime, keeping your production lines running smoothly.
- Comprehensive Services: Specialized centers often offer a wide range of services, from diagnostics and repairs to upgrades and programming.
Key Benefits of Having a Dedicated PLC Repair Center
Having a dedicated PLC repair center on speed dial can yield numerous benefits:
- Cost Efficiency: Regular maintenance and prompt repairs can prevent costly replacements and downtime.
- Enhanced System Performance: Regular servicing ensures that your PLCs operate at peak efficiency, leading to better overall performance of your automation system.
- Access to Parts: Specialized centers typically have access to genuine replacement parts, ensuring that your repair meets the manufacturer's specifications.
What to Look for in a PLC Repair Center
Choosing the right PLC repair center is crucial for the longevity of your automation systems. Here are some factors to consider:
- Credentials: Ensure the center has qualified technicians with adequately recognized certifications.
- Track Record: Look for reviews or case studies showcasing successful repairs and satisfied clients.
- Service Scope: The center should provide a variety of services beyond just repairs, such as programming, training, and consultation.
- Warranty: A reputable service provider should offer warranties on their repairs and parts.
Common PLC Issues and Solutions
Understanding the common issues that can arise with PLCs can help businesses be better prepared. Below are some typical problems and their solutions:
1. Power Supply Issues
Power supply problems can lead to the failure of the PLC to start or cause it to operate erratically. Always check for:
- Voltage irregularities: Ensure your power supply is stabilized.
- Overheating: Make sure the environment is suitable for the PLC’s operating temperature.
2. Input/Output Module Failures
Input or output module failures can disrupt the communication between the PLC and the connected devices. Solutions include:
- Inspecting connections: Loose connections can often be the culprit.
- Replacing faulty modules: Immediate replacement can prevent further operational issues.
3. Corrupted or Missing Program
If a PLC's program becomes corrupted, it can lead to operational delays. To remedy this, consider:
- Backing up your programs: Regular backups can save time and money in the long run.
- Consulting with the repair center: Experts can recover or restore the program.
The Process of PLC Repair
Understanding the process involved in PLC repair at a specialized center can provide peace of mind:
- Initial Assessment: The repair center will conduct a diagnostic assessment to identify all issues.
- Repair Procedure: Once issues are identified, approved repairs will be performed using high-quality parts.
- Testing: After repairs, the PLC is extensively tested to ensure functionality before returning it to the client.
- Documentation: A comprehensive report detailing the repairs made and recommendations for future maintenance is provided.
Importance of Choosing a Local Electronic Components Distributor
Aside from PLC repair services, having a trusted electronic components distributor can be a game changer for your business. Here are several benefits of having a local distributor:
- Immediate Supply: Local distributors can provide quick access to necessary components, reducing lead times.
- Personalized Service: Close proximity allows for better relationships and tailored service to meet specific business needs.
- Stock Availability: A well-stocked distributor will have a range of components on hand, minimizing delays in repairs and service situations.
Choosing QF Automation: Your Partner in Success
At QF Automation, we pride ourselves on being more than just a PLC repair center. We offer a comprehensive range of services, including electronic component distribution across Canada. Our experienced technicians are dedicated to ensuring that your automation systems are efficient, reliable, and ready to meet the demands of today's market.
Commitment to Quality
We use only high-quality parts and ensure our processes meet industry standards. Our commitment to quality means that when you choose QF Automation, you choose peace of mind.
Wide Range of Products
As a trusted electronic components distributor in Canada, we provide a vast inventory of products for all your automation needs. From basic components to advanced automation systems, we facilitate our clients with all necessary resources.
Expert Guidance and Support
Our team not only repairs PLCs but also provides expert guidance on service optimization and future upgrades. We believe in partnering with you for long-term success.
Conclusion: Elevate Your Automation with Expert Services
In conclusion, selecting the right PLC repair center and electronic components distributor can significantly influence your industrial operations. Trusting experts like QF Automation ensures that your automation systems are in capable hands, allowing you to focus on growth and productivity. With our unwavering commitment to quality and customer satisfaction, we stand ready to meet your automation challenges, providing the service and support your operations require.
For more information or to schedule a consultation, please visit our website at qfautomation.com today!