The Importance of Understanding LOLER Regulations
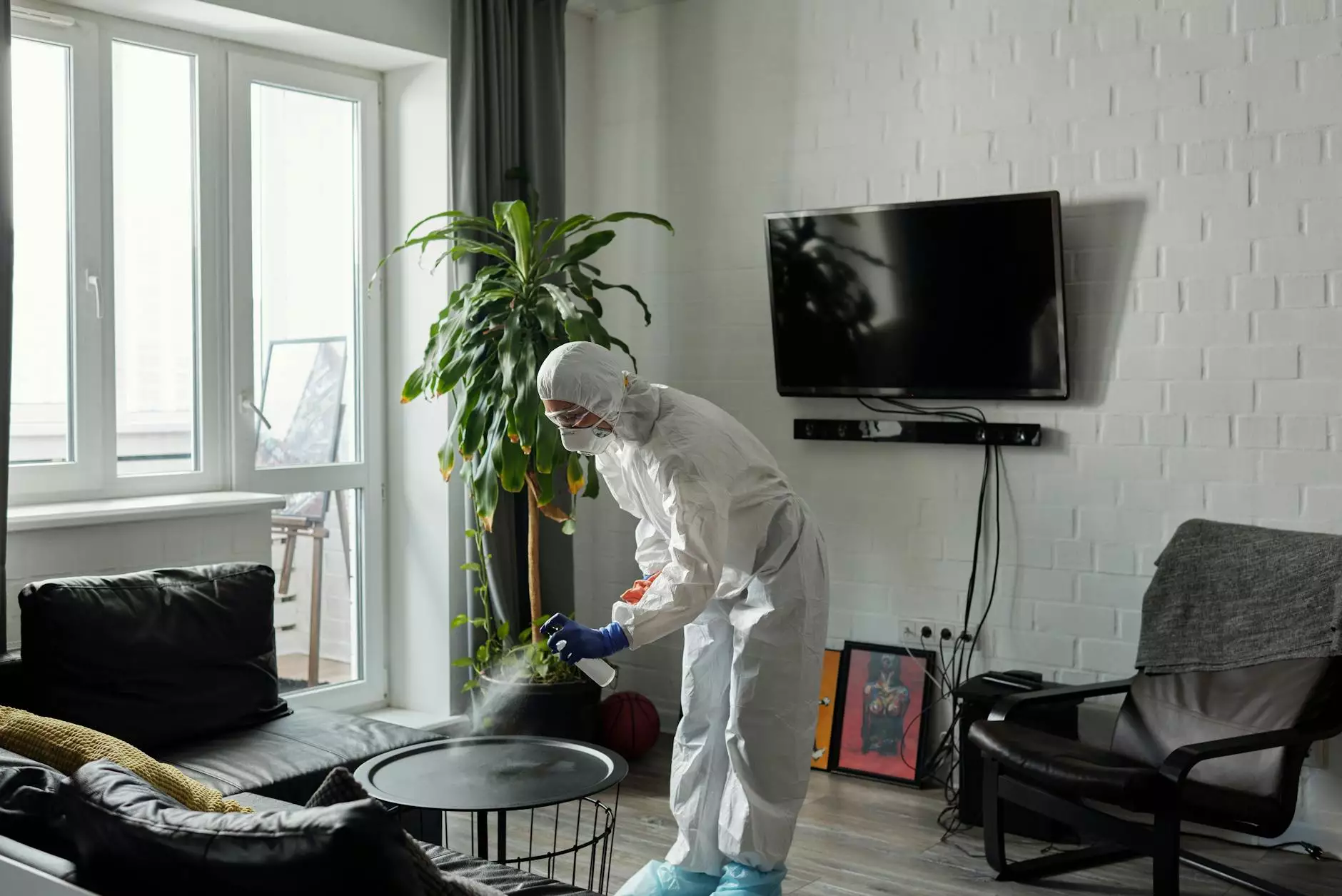
In today's dynamic business environment, workplace safety is not just a legal requirement; it is a fundamental aspect of operational excellence. One significant component that businesses must understand is the LOLER regulations. This article aims to provide a detailed overview of LOLER regulations, their significance in the realm of lifting operations, and how adhering to them can enhance workplace safety, particularly in the home and garden sectors.
What Are LOLER Regulations?
The Lifting Operations and Lifting Equipment Regulations 1998 (LOLER) are a set of statutory regulations that govern the safe use of lifting equipment in the workplace. These regulations were established to minimize risks associated with lifting operations, ensuring that lifting equipment is safe to use and properly maintained. They are integral to promoting safety in various industries, including construction, manufacturing, and even home and garden services.
Key Objectives of LOLER Regulations
The LOLER regulations aim to:
- Ensure Equipment Safety: All lifting equipment must be fit for purpose, maintained in a safe condition, and inspected regularly.
- Minimize Risks: By ensuring that lifting operations are planned, supervised, and conducted safely, the potential for accidents is greatly reduced.
- Protect Workers: The health and safety of employees are paramount, and these regulations help in reducing injuries related to lifting tasks.
- Enhance Accountability: Employers are legally obligated to ensure compliance with LOLER, fostering a culture of responsibility and safety.
Key Definitions and Terminology
Understanding key terms associated with LOLER is essential for effective compliance:
- Lifting Equipment: Any equipment used for lifting or lowering loads (e.g., cranes, hoists, lifts).
- Work Equipment: Any machinery, appliance, or tool used at work, including lifting equipment.
- Operator: A person who directly handles the lifting equipment and operates it.
- Thorough Examination: A detailed inspection of lifting equipment conducted by a competent person.
Compliance with LOLER Regulations
Compliance with LOLER is mandatory for all businesses that use lifting equipment. Here are the steps businesses should take to ensure they meet LOLER standards:
1. Identify and Categorize Lifting Equipment
Businesses must identify all lifting equipment used in their operations and categorize it based on its use and risk level. This assessment helps in understanding which equipment requires regular inspection and maintenance.
2. Conduct Regular Inspections
It is crucial to perform thorough examinations of lifting equipment at specified intervals. This examination must be carried out by a competent person, ensuring that all safety aspects are evaluated.
3. Maintain Proper Records
Keeping detailed records of inspections, maintenance, and repairs is essential for compliance. This documentation not only aids in regulatory adherence but also enhances accountability among staff.
4. Train Employees
Training and competency are vital for ensuring that employees understand how to operate lifting equipment safely. Training should cover the risks associated with lifting operations, proper equipment handling, and emergency procedures.
5. Ensure Safe Operating Procedures
Establishing safe operating procedures for lifting activities can help mitigate risks. These procedures should be documented, communicated, and enforced among all staff involved in lifting operations.
The Business Benefits of Complying with LOLER Regulations
While compliance with LOLER regulations is primarily mandated for safety, it also brings numerous business advantages:
- Reduced Risk of Accidents: Compliance minimizes the likelihood of accidents and injuries, creating a safer working environment.
- Enhanced Reputation: Businesses that prioritize safety can enhance their reputation, attracting customers and clients who value safe practices.
- Financial Savings: Reducing accidents and equipment downtime leads to significant cost savings in terms of compensation claims, repairs, and loss of productivity.
- Legal Compliance: Adhering to LOLER helps businesses avoid legal penalties and liabilities associated with workplace injuries.
Industry-Specific Applications of LOLER Regulations
LOLER regulations are applicable across various sectors. Here’s how they are relevant in specific industries:
1. Construction Industry
The construction sector frequently utilizes cranes, hoists, and other lifting equipment. Compliance with LOLER regulations is crucial to prevent accidents that could lead to severe injuries or fatalities. Regular inspections and proper training ensure that operators can handle equipment safely.
2. Manufacturing Sector
In manufacturing, lifting equipment is often used for transporting heavy materials. Adhering to LOLER regulations protects workers from accidents and enhances operational efficiency. Businesses are encouraged to integrate safety training into their employee onboarding processes.
3. Home and Garden Services
For businesses operating in the home and garden sectors, such as landscapers and gardeners, lifting regulations also apply. Equipment like forklifts or hoists, used for transporting heavy materials or equipment, must meet LOLER standards to ensure worker safety.
Conclusion: The Path Forward
The LOLER regulations play an essential role in promoting safety across all sectors, particularly in environments where lifting equipment is used. Businesses are encouraged to take proactive steps towards compliance, as the benefits extend beyond legal requirements—they foster a culture of safety, enhance efficiency, and protect the workforce. As a company operating in the home and garden sector, staying informed about LOLER regulations not only safeguards employees but also strengthens your business reputation in a competitive marketplace.
Invest in safety training, regular inspections, and proper recordkeeping to ensure your compliance and contribute to a safer work environment. By prioritizing adherence to LOLER regulations, you position your business for success while protecting your most valuable asset—your employees.