Emergency Escape Breathing Apparatus Inspection: An In-Depth Analysis
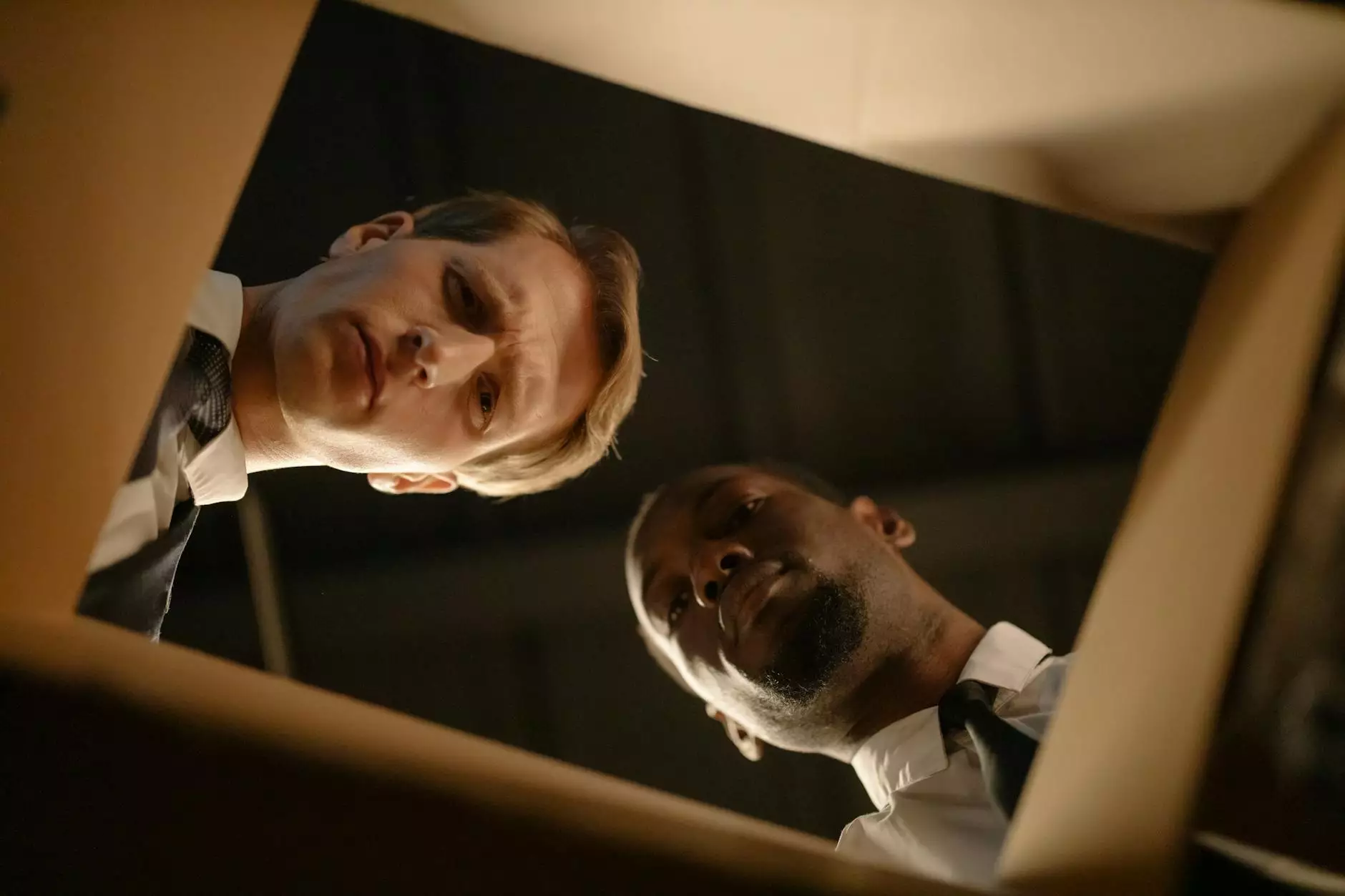
The safety of employees is paramount in any industry, and this is particularly true in areas where risks abound. In sectors like special education, ensuring that personnel are adequately equipped to handle emergencies is a legal requirement as well as a moral one. One crucial aspect of this safety is the proper inspections of emergency escape breathing apparatus (EEBA). In this article, we will explore the intricacies of EEBA inspection, its significance, the process, key regulations, and best practices to ensure compliance and safety in the workplace.
Understanding the Emergency Escape Breathing Apparatus (EEBA)
Emergency Escape Breathing Apparatus (EEBA) refers to specialized breathing devices designed to provide clean air to individuals who may be exposed to hazardous conditions. EEBAs are widely used in various sectors, including firefighting, mining, and even in educational settings, especially where chemical safety is a concern.
- Definition: An EEBA is a self-contained breathing apparatus designed for short-term use during escape situations.
- Components: It typically includes a compressed air cylinder, a pressure regulator, and a face mask.
- Purpose: It aims to protect users from inhaling harmful substances during emergencies.
The Importance of EEBA Inspection
Regular inspections of emergency escape breathing apparatuses are crucial for the following reasons:
- Compliance: Many regulations mandate that businesses conduct regular inspections of safety equipment.
- Operational Readiness: Inspections ensure that EEBAs are in functional condition and ready to use at a moment's notice.
- Employee Confidence: Knowing that safety measures are in place boosts employee morale and confidence in the workplace.
- Risk Mitigation: Proper inspections help identify equipment that may pose risks, preventing potential injuries.
In the realm of special education businesses, where unique hazards may exist, EEBA inspections become even more critical to ensure that staff is prepared to handle emergencies effectively.
Regulations Governing EEBA Inspections
Various agencies have set forth regulations regarding the inspection and maintenance of EEBAs. Understanding these regulations is vital for business compliance:
1. OSHA Regulations
The Occupational Safety and Health Administration (OSHA) regulates workplace safety, including the use of personal protective equipment like EEBAs. Employers are required to:
- Maintain and inspect EEBAs as per manufacturer’s guidelines.
- Keep inspection records for a specified period.
- Train employees on the proper use of EEBAs.
2. NFPA Standards
The National Fire Protection Association (NFPA) also plays a role in setting standards for EEBAs, particularly those used in fire safety scenarios. Compliance with NFPA 1981 is essential, which includes:
- Performance requirements for EEBAs.
- Maintenance and inspection protocols.
3. Manufacturer Guidelines
Most EEBA manufacturers provide detailed guidelines on inspection and maintenance. Following these guidelines is essential to uphold the warranty and guarantee that the equipment functions as intended.
Process of Inspecting Emergency Escape Breathing Apparatus
The inspection process for EEBAs consists of several key steps designed to ensure the apparatus is in proper working order:
1. Visual Inspection
Inspectors should conduct a thorough visual check of the EEBA. Look for:
- Physical damage such as cracks or dents in the cylinder or mask.
- Corrosion on metal components.
- Integrity of the straps and harnesses.
2. Functional Testing
After the visual check, a functional test should be carried out, which includes:
- Checking the pressure gauge for proper readings.
- Testing the regulator for air flow issues.
- Ensuring the mask forms a proper seal.
3. Maintenance Checks
Maintenance will typically involve:
- Cleaning the apparatus per manufacturer instructions.
- Recharging or replacing air cylinders as needed.
- Inspecting and replacing filters if applicable.
4. Documentation
Record keeping is essential. Ensure that all inspections, maintenance activities, and any repairs done on the EEBA are documented accurately. This documentation should include:
- Date of inspection.
- Details of any findings and actions taken.
- Name and signature of the inspector.
Best Practices for EEBA Inspections
In addition to following regulations, there are best practices to adopt that can enhance the effectiveness of your EEBA inspections:
- Regular Training: Conduct routine training sessions for staff to ensure they are familiar with the inspection protocols and the importance of EEBAs.
- Develop a Schedule: Establish a consistent schedule for inspections that meets or exceeds local regulations and standards.
- Utilize Checklists: Implement inspection checklists to standardize the process and ensure no step is overlooked.
- Engage Experts: Consider hiring professionals for periodic thorough inspections and maintenance, especially for specialized equipment.
Conclusion
The need for emergency escape breathing apparatus inspection cannot be overstated, especially in industries that operate under the potential threat of hazardous conditions, such as special education. By understanding the importance of inspections, adhering to regulations, and following best practices, businesses can significantly enhance the safety of their environments and ensure peace of mind for their employees.
Investing time and resources into proper EEBA inspections not only fulfills legal obligations but also demonstrates a commitment to employee safety. As businesses continue to evolve, focusing on robust safety protocols, including the regular inspection of emergency escape breathing apparatus, remains a cornerstone of workplace safety culture.
Contact Us
For more information on how to comply with EEBA regulations and ensure your apparatus is ready for emergencies, visit us at h2sonlinetraining.com.